Product Introduction:
High activity rotary lime kiln is a type of kiln that used for lime production. It is a rotary kiln that uses rotation and internal combustion to complete lime calcining operations. It is the main production line for highly active lime products. The successful industrial application of energy-saving and environmentally friendly active lime rotary kiln with vertical preheater and vertical cooler has broken the traditional lime production method.
The rotary lime kiln usually consists of a feeding system, a preheating system, a calcining system, a cooling system, a finished product system, a kiln tail flue gas system, etc. Rotary kiln is the main processing equipment for lime production in large enterprises such as steel plants, alumina plants, and calcium carbide plants.
Product Advantages:
01
It is very suitable for large-scale activated lime production lines with higher capacity. The production capacity can reach 150-1200 tpd.
02
The quality of lime is better with higher activity and larger specific surface area, which is currently the most important auxiliary material in steelmaking, aluminum making, calcium carbide and other related industries.
03
The rotary kiln has a simple structure, strong controllability, and is convenient for operation and maintenance.
04
It can burn fine-grained limestone and make better use of mine resources.
05
A rotary kiln with a vertical preheater installed at the end of the kiln can make full use of the exhaust gas at the end of the kiln to preheat the limestone, greatly reducing fuel consumption.
06
Industrial waste gas can be fully utilized as fuel for lime burning, such as blast furnace gas, converter gas, carbide furnace exhaust gas, blue charcoal furnace exhaust gas, etc.
07
The kiln head adopts the integrated design and construction of vertical cooler and kiln head cover, which has a small footprint, good sealing and good cooling effect.
08
Using pulse bag dust collector for dust removal, and the emission concentration is less than 10mg/Nm3.
09
High level of automation, reduce on-site operators, and make labor efficiency higher.
Main Technical Specifications:
Model |
Capacity/t/d |
Rotating Speed/r/min |
Main Reducer Model |
Main Motor |
Motor Powder/kw |
|
Model |
Power |
|||||
Φ2.5×40 |
150 |
0.62-1.5 |
ZS125-2-I |
Z2-92 |
40 |
143.6 |
Φ2.8×42 |
200 |
0.5-2.503 |
ZSY355-50-I |
Z2-101TH |
55 |
199.8 |
Φ3.0×46 |
250 |
0.67-3.76 |
NZZL130-15-I |
ZSN4-280-091B |
110 |
237 |
Φ3.2×42 |
300 |
0.674-3.37 |
MSY56-28-II |
ZSN4-280-21B |
160 |
252.4 |
Φ3.6×56 |
400 |
0.4-1.5 |
ZSY500-40 |
ZSN-315-072 |
250 |
387 |
Φ3.8×58 |
500 |
0.4-1.5 |
ZSY500-40 |
ZSN-315-072 |
250 |
412 |
Φ4.0×60 |
600 |
0.396-3.96 |
ZSY630-35.5-I |
ZSN4-355-092 |
315 |
487.51 |
Φ4.0×64 |
800 |
0.398-3.98 |
ZSY710-35.5 |
ZSN4-355-12 |
420 |
598.5 |
Φ4.88×70 |
1000 |
0.58-3.46 |
ZSY710-28-V |
Z4-400-32 |
550 |
821 |
Process Flow Chart:
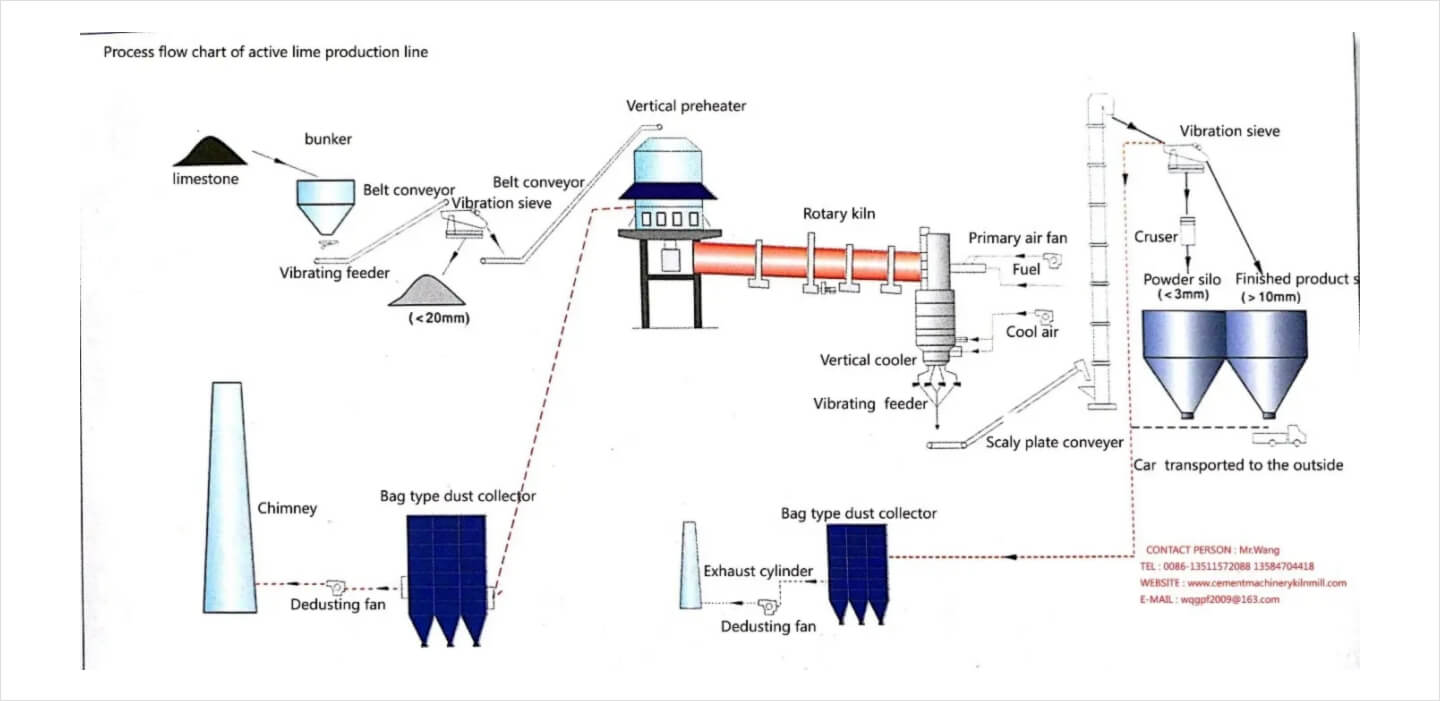
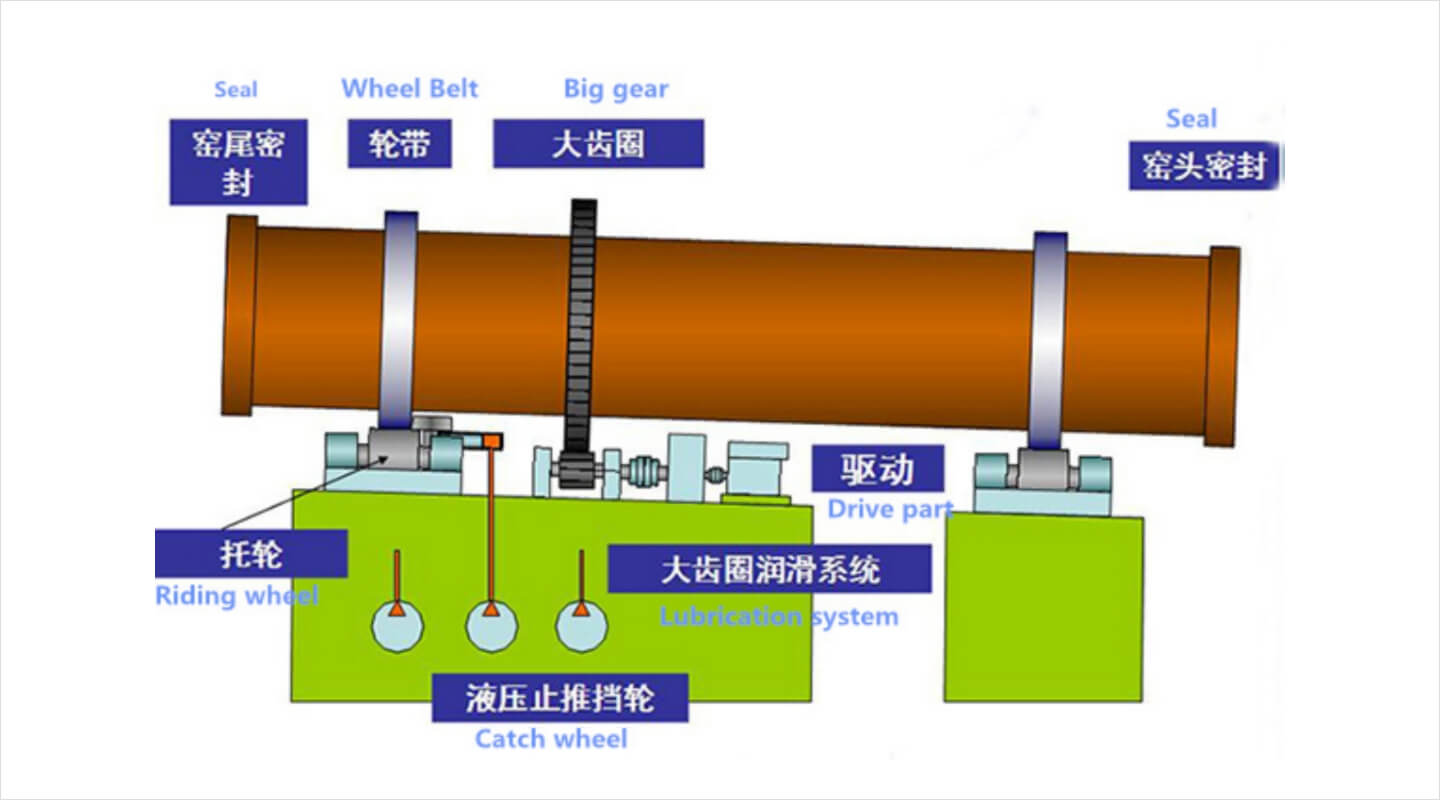
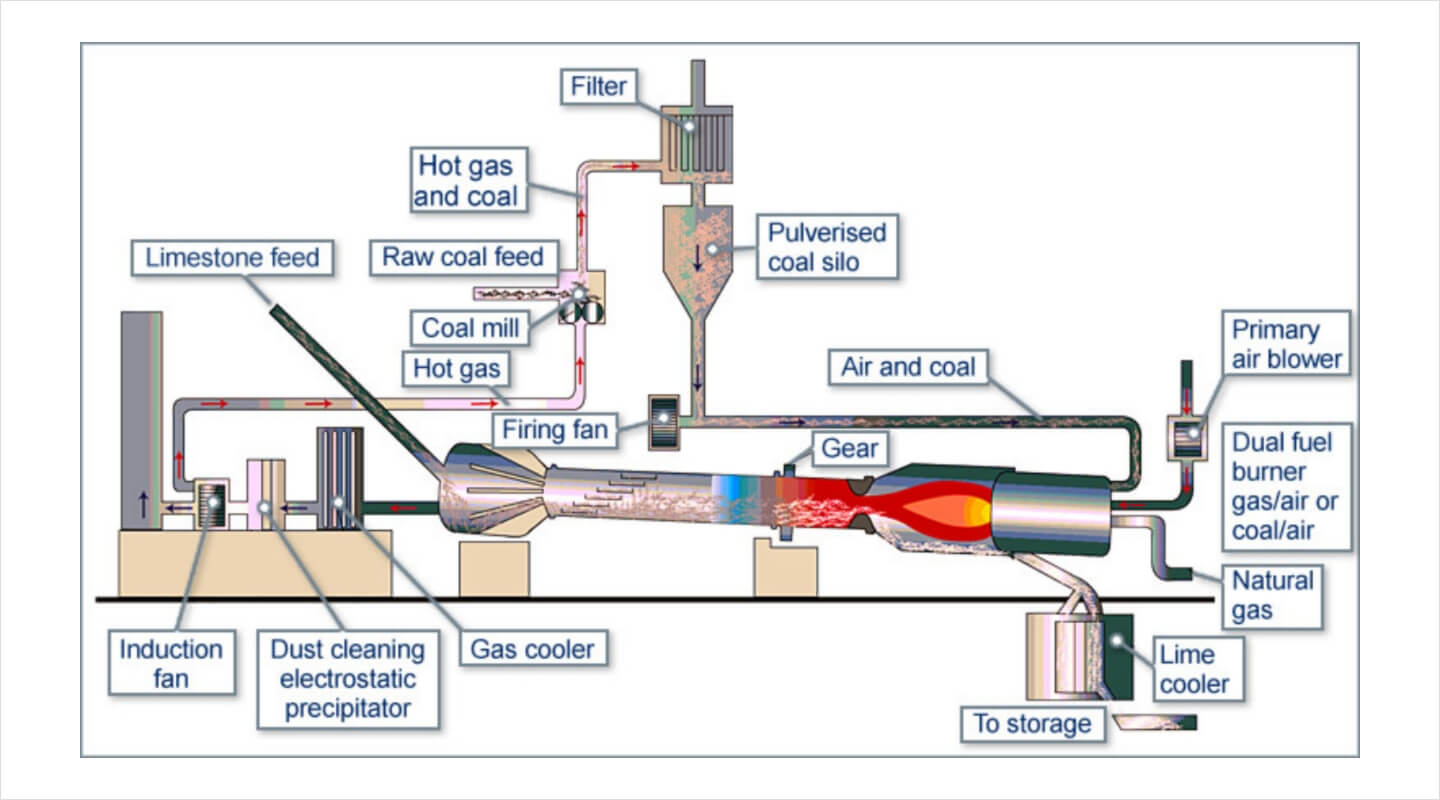